Which sensors are used in the data loggers?
We use the following internal sensors in our data loggers:
-
Temperature sensors: e.g. digital temperature sensors of the NXP series. These sensors have a measuring range of -40 to +100°C.
-
Humidity sensors: e.g. humidity sensors from Sensirion. This sensor has a measuring range of 0 to 100% relative humidity.
-
Pressure sensors: The data loggers use a piezo-resistant MEMS pressure sensor. The pressure sensor has a measuring range of 260 to 1,260 mbar (hPa) absolutely.
-
3 axis acceleration senors: MEMS sensors are used in current data loggers (measurement accuracy).
-
Light sensor
In addition, there are the following wired external sensors:
-
Temperature sensors: e.g. combined temperature-humidity sensors from Sensirion. These sensors have a measuring range of -40 to +125 °C.
-
Humidity sensors: e.g. combined temperature-humidity sensors from Sensirion. These sensors have a measuring range of 0 to 100% relative humidity.
-
Pressure sensors: A piezo-resistant MEMS pressure sensor is used for the external sensors. The pressure sensor has a measuring range of 260 to 1,260 mbar (hPa) absolutely.
-
3 axis acceleration sensors: Current data loggers use MEMS sensors with measuring ranges up to 64 g.
What are the structure and functioning of the sensors?
-
Digital temperature sensor: Temperature sensors are electrical and electronic components that, as sensors, make the temperature measurable via a specific electrical signal. These are integrated semiconductor temperature sensors or solid state circuits. Depending on the temperature, they produce a current, a voltage or a digital signal.
-
Humidity sensor: In addition to the resistive method, the capacitive measuring principle has established itself as a standard and proven itself in recent years. In this principle, the sensor element is constructed from a capacitor. The dielectric is a polymer that absorbs or releases water proportionally to the relative humidity of the environment and thus changes the capacitance of the capacitor. This capacity change can be measured via an electronic circuit and the relative humidity can be determined. A patented “micro-machined” finger electrode system serves as capacity for humidity sensors. Different protective and polymer cover layers are applied to the electrode system in several finishing steps. At the same time, these protect the sensor from disturbing influences.
- Pressure sensor: A pressure sensor is an electrical component that converts the physical measure of pressure into an electrical signal. This can be read and interpreted by a controller or an ECU, so that an appropriate action can be taken automatically.
Capacitive pressure sensors consist of two capacitors in a silicon chip. If the pressure in a system increases, the distance between the two capacitors changes to an intermediate membrane. As a result, their capacities, i.e. their ability to absorb and store electric energy, also change. This can be measured to measure the pressure.
Inductive pressure transducers consist of a membrane on which an iron core is located. If the pressure changes, the membrane deforms and the iron core moves. Its position influences the inductance of two coils, which can be measured by measurement.
Piezo-electric pressure sensors use the piezoelectric effect to detect forces. This is made possible by their special properties. The deformation of a crystal produces an electrical voltage that can then be evaluated and interpreted. A pressure sensor first converts the pressure in a system into a force via a movable membrane.Piezo-resistive pressure sensors record the pressure in a room or medium with strain gauges or semiconductor chips. A deformation of the elements leads to a change in the electrical resistance. This can then be evaluated metrologically to record the pressure.
-
Acceleration sensor: An accelerometer (also known as an accelerometer, accelerometer, vibration sensor, vibration sensor, accelerometer, B-meter or G-sensor) is a sensor that detects the inertial force acting on a test mass. Two types of acceleration sensors are distinguished, capacitive and piezo-electric sensors.
A capacitive acceleration sensor consists of two adjacent plate capacitors using a common middle plate. The movable middle plate is designed as a spring-loaded pendulum. If the sensor is accelerated, this central plate moves. The capacitance ratio of the two capacitors changes.
Piezo-electric acceleration sensors work with piezo-electric crystals to detect forces. A mass attached to the piezo ceramics acts on the entire system during an acceleration. Due to the acting force, the piezo crystal deforms and generates an electrical voltage that can be processed. Single-crystalline sensors are mostly made of silicon and are often integrated into miniaturized MEMS (Micro Electrical Mechanical System) chips.
Will the pressure sensors be calibrated?
Our pressure sensors are calibrated over the entire specified pressure range. The measured values of the pressure sensor to be calibrated are compared with those of a more precise, traceable reference device of the German Accreditation Body. Subsequently, the measurement parameters in the device and sensor are adjusted and a measurement protocol of the factory calibration is created.
Overpressure in the active part of the transformer prevents the penetration of dirt particles. In order to detect a pressure drop, we use an external pressure sensor in conjunction with the MONILOG® data logger, which is inserted into the housing wall.
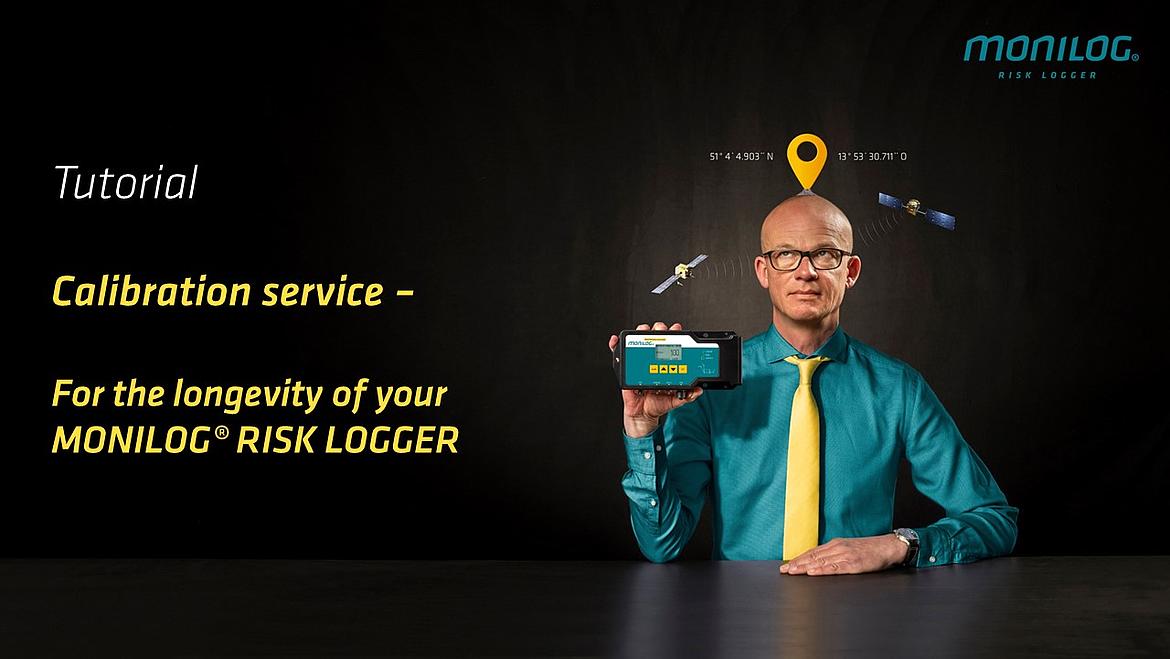
Fitting products
EnDaLsmart
Compact logger, especially suitable for monitoring large transports. With an integrated GPS receiver and inclination sensor. Also approved for air freight.
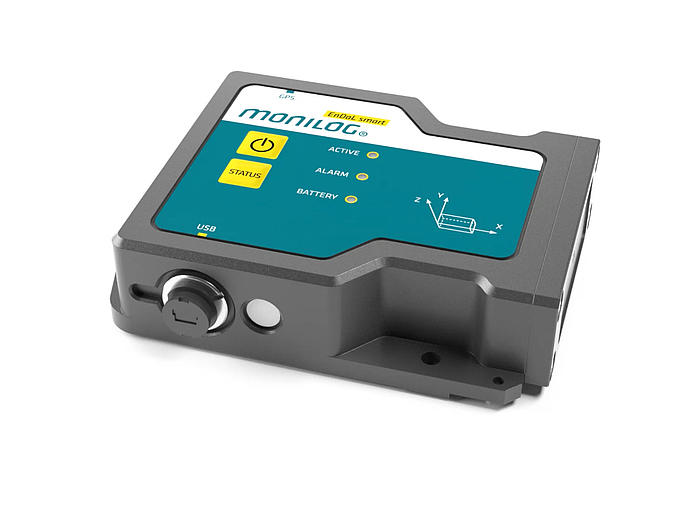